Expert Packaging Machine Repair for Seamless Production Efficiency
Expert Packaging Machine Repair for Seamless Production Efficiency
Blog Article
Quick and Reliable Product Packaging Equipment Repair Work Solutions to Minimize Downtime
In the competitive landscape of production, the performance of product packaging operations pivots on the integrity of machinery. Quick and reliable fixing solutions are essential in minimizing downtime, which can lead to substantial monetary losses and operational troubles.
Value of Timely Services
Prompt repair services of packaging equipments are vital for keeping operational performance and minimizing downtime. In the fast-paced setting of manufacturing and product packaging, even small malfunctions can lead to considerable delays and performance losses. Addressing problems immediately makes certain that devices operate at their ideal ability, consequently safeguarding the flow of procedures.
Moreover, prompt and regular upkeep can protect against the acceleration of minor problems right into major break downs, which usually incur higher repair costs and longer downtimes. A positive strategy to machine fixing not only protects the integrity of the equipment but likewise boosts the overall reliability of the assembly line.
Furthermore, prompt repairs add to the durability of product packaging machinery. Makers that are serviced without delay are less likely to deal with extreme damage, enabling organizations to optimize their investments. This is particularly vital in sectors where high-speed packaging is vital, as the demand for regular performance is extremely important.
Advantages of Reliable Company
Trustworthy solution providers play a critical function in making certain the smooth operation of product packaging machines. Their know-how not only boosts the efficiency of fixings but also contributes considerably to the long life of devices. Trusted provider are furnished with the technical understanding and experience required to identify problems properly and implement reliable services rapidly. This reduces the threat of persisting problems and guarantees that machines operate at optimum performance degrees.
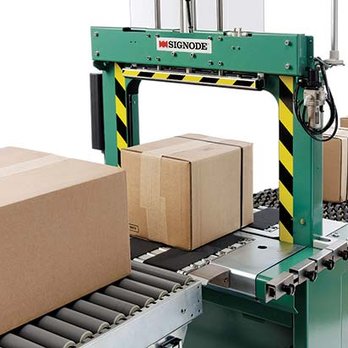
Furthermore, a trustworthy company supplies detailed support, consisting of training and advice for personnel on machine operation and maintenance finest methods. This not only equips employees however likewise grows a culture of safety and security and efficiency within the company. Generally, the advantages of involving dependable company prolong past prompt fixings, favorably impacting the whole functional operations of packaging processes.
Common Product Packaging Device Problems
In the world of product packaging operations, numerous problems can jeopardize the efficiency and functionality of equipments (packaging machine repair). One more common concern is misalignment, which can trigger jams and irregular product packaging, impacting product top quality and throughput.
Electric issues can likewise disrupt packaging operations. Malfunctioning electrical wiring or malfunctioning sensors may lead to irregular machine habits, creating hold-ups and enhanced operational prices. Furthermore, software program problems can prevent the machine's programs, bring about operational inadequacies.
Inconsistent item circulation is an additional important concern. This can emerge from variations in item form, weight, or size, which may impact the machine's ability to deal with products properly. Ultimately, insufficient training of drivers can aggravate these troubles, as untrained workers may not acknowledge very early signs of malfunction or may abuse the devices.
Addressing these usual packaging device concerns quickly is necessary to keeping productivity and guaranteeing a smooth operation. Routine evaluations and positive upkeep can significantly reduce these problems, promoting a reliable product packaging setting.
Tips for Reducing Downtime
To decrease downtime in product packaging operations, implementing a proactive upkeep method is crucial. Frequently set up maintenance checks can recognize prospective issues prior to they intensify, making sure devices operate successfully. Establishing a regimen that includes lubrication, calibration, and examination of important parts can dramatically lower the get redirected here regularity of unforeseen malfunctions.
Educating staff to operate machinery properly and recognize early indication of breakdown can likewise play an important role. Equipping drivers with the expertise to perform basic troubleshooting can avoid minor concerns from causing major hold-ups. Furthermore, maintaining a well-organized supply of vital spare components can accelerate repair services, as waiting on parts can lead to extended downtime.
Furthermore, documenting maker performance and upkeep activities can assist identify patterns and persistent issues, permitting targeted treatments. Incorporating advanced surveillance technologies can provide real-time data, enabling anticipating upkeep and lessening the threat review of sudden failings.
Last but not least, fostering open communication in between drivers and upkeep groups ensures that any type of abnormalities are quickly reported and resolved. By taking these aggressive actions, businesses can enhance functional effectiveness and dramatically lower downtime in product packaging processes.
Choosing the Right Repair Work Service
Choosing the appropriate repair solution for packaging machines is a critical decision that can substantially influence operational performance. Begin by reviewing the supplier's experience with your specific kind of product packaging equipment.
Next, think about the solution provider's credibility. Seeking feedback from other businesses within your sector can supply understandings right into dependability and top quality. Certifications and collaborations with identified devices manufacturers can likewise show a dedication to excellence.
In addition, evaluate their response time and schedule. A provider who can offer prompt assistance minimizes downtime and keeps manufacturing flow constant. It's also vital to ask about guarantee and service warranties, which can mirror the self-confidence the service provider has in their job.

Verdict
To conclude, the significance of trustworthy and quick packaging maker repair service solutions can not be overstated, as they play see here now a vital duty in reducing downtime and guaranteeing operational efficiency. By prioritizing prompt repair work and picking reputable solution suppliers, services can successfully preserve and deal with usual problems efficiency. Executing aggressive maintenance practices and buying team training more boosts the durability of packaging machinery. Eventually, a calculated strategy to fix services cultivates an extra resistant manufacturing setting.
Prompt repair work of product packaging equipments are crucial for preserving operational performance and minimizing downtime.In addition, prompt repair work add to the long life of packaging machinery. In general, the benefits of engaging reputable solution companies extend beyond prompt repair work, favorably impacting the entire operational workflow of packaging processes.

Report this page